Tammer Brands: From manual to magical
About Tammer Brands
Founded in 1954, Tammer Brands is a family-owned wholesale company based in Tampere, Finland. Over the years, the company has grown into one of Northern Europe's top consumer goods enterprises. With a mix of over 50 brands and more than 20,000 products, from household essentials to items that enhance everyday life, Tammer Brands is dedicated to providing high-quality products to its customers.
Tammer Brands' mission centers on understanding the varied needs of daily life, ensuring that each product not only benefits the end-user but also supports the businesses of their partners. This commitment to quality and innovation has positioned Tammer Brands as a trusted name in the industry, continually striving to improve people's quality of life through their extensive product range.
"What I really like is that I can see the status from my phone – what's happening and what the actual real-time situation is in the warehouse operations."Tiina Nygård, Chief Supply Chain Officer, Tammer Brands |
InstallationLocationTampere, Finland |
In this videoTiina Nygård Joni Viikki |
Challenges in warehouse management before Bitlog WMS
Before implementing Bitlog WMS, Tammer Brands faced several challenges in their warehouse operations:
-
Manual processes slowing down efficiency: Orders had to be manually compiled into picking lists, sorted in a separate area, and then processed individually.
-
Limited workload visibility: There was no real-time overview of warehouse activity, leading to delays and inefficiencies.
-
Fragmented data management: Information had to be manually entered into different Excel sheets and systems to get an overview of operations.
-
Production delays: The lack of automated order handling led to bottlenecks in production and fulfillment.
Tammer Brands’ warehouse processes were heavily reliant on manual work, which created inefficiencies across operations. Picking, sorting, and tracking orders were time-consuming tasks that required constant supervision. Without a centralized system for managing workload and inventory, delays became common, impacting both productivity and customer satisfaction.
Additionally, managing data across multiple programs made it difficult to get an accurate real-time view of warehouse operations, further complicating decision-making and planning.
"We had to take all the small orders, make them into one picking list manually, pick the products, take it all to a separate area, and sort all the orders, again, manually. We couldn't see how big of a workload we had and we struggled with delays," says Joni Viikki, Logistics Manager at Tammer Brands.
How Bitlog WMS has solved Tammer Brands' challenges
To address these inefficiencies, Tammer Brands chose Bitlog WMS for its modern interface, automation capabilities, and strong development team.
-
Real-time warehouse visibility: Supervisors can now track warehouse operations live from their mobile devices.
-
Automation of key processes: Orders are now automatically grouped and scheduled for picking.
-
Scalable and intuitive: The user-friendly interface allows new employees to get up to speed quickly.
-
Collaborative development: Bitlog’s responsive team quickly implemented custom improvements, such as scanner optimizations, in just two weeks.
"What I really like is that I can see the status from my phone – what's happening and what the actual real-time situation is in the warehouse operations," says Tiina Nygård, Chief Supply Chain Officer at Tammer Brands.
Bitlog WMS provided Tammer Brands with a modern, efficient solution for warehouse management. The real-time visibility into warehouse operations allowed supervisors to track progress and address potential issues before they caused disruptions. Automation significantly reduced manual workload, enabling employees to focus on more critical tasks. The intuitive user interface made onboarding and daily operations smoother, while Bitlog’s willingness to develop customized features ensured that the system aligned perfectly with Tammer Brands’ needs.
"The feeling we got from Bitlog was that we were talking to a company that wanted to develop together with us, that really wants to focus on WMS and be one of the best in warehouse processes," Joni adds.
Results with Bitlog WMS
Since implementing Bitlog WMS, Tammer Brands has seen significant improvements:
-
Faster picking and incoming goods handling: The picking process is now much more efficient.
-
Greater responsibility for warehouse workers: Supervisors can delegate more tasks, improving overall workflow.
-
Improved order consolidation: Freight costs have been reduced due to better order grouping.
-
Enhanced production management: Warehouse supervisors can now use an iPad in the production area to provide real-time support.
-
Elimination of delays: Processes are smoother, with no waiting times for printing picking lists or system delays.
The impact of Bitlog WMS on Tammer Brands’ warehouse operations has been transformative. With improved efficiency in picking and incoming goods handling, order fulfillment times have significantly decreased. The automation of tasks has allowed warehouse staff to take on more responsibility, reducing dependency on supervisors for routine processes.
"Before, we could pick only one order at a time. Now, we can pick up to 24 orders at a time!" Says Joni, and continues: "We have also managed to lower freight costs because we now have much better order consolidation."
The much improved order consolidation has led to cost savings on freight, while the ability to manage production in real time has enhanced overall workflow. By eliminating delays and streamlining processes, Bitlog WMS has helped Tammer Brands achieve a higher level of operational efficiency.
"The feeling we got from Bitlog was that we were talking to a company that wanted to develop together with us, that really wants to focus on WMS and be one of the best in warehouse processes"Joni Viikki, Logistics Manager, Tammer Brands |
Why Tammer Brands Recommends Bitlog WMS
For Tammer Brands, Bitlog WMS has been a game-changer, providing an intuitive, efficient, and scalable solution for warehouse management. And when asked why they would recommend Bitlog to other companies, Tiina and Joni summarizes it into three main reasons:
-
The user-friendly interface. Employees quickly adapt to the system, reducing onboarding time. Joni says: "I really like the user interface – it’s so easy to use. When we get new people, they can start working with Bitlog WMS really fast."
-
The optimized warehouse processes. Bitlog WMS balances advanced functionality with simplicity. Tiina and Joni agrees that "there are enough features, but not too many. It's easy to use, and there's a logic to how it works."
-
Bitlog as a committed development partner. The Bitlog team actively collaborates to continuously improve the system.
Tammer Brands recommends Bitlog WMS to companies looking for a reliable warehouse management solution. The user-friendly interface ensures a smooth learning curve for employees, while the optimized processes make daily warehouse operations more efficient.
Bitlog’s commitment to continuously improving its system and working closely with customers sets it apart from other WMS providers. For Tammer Brands, Bitlog WMS is more than just a system—it’s a long-term partner in warehouse efficiency and growth.
You might also like:
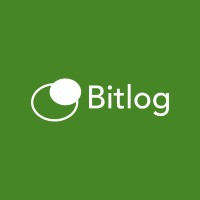
Story by
The Bitlog Team