Care of Carl: 40% more efficient in the warehouse
About Care of Carl
Care of Carl is a well-established retailer of men's clothing online, focusing on high quality, style, and service. Since its inception, they have aimed to provide their customers with an exclusive shopping experience through a carefully curated selection and personalized service. With a dedication to offering the best in men's fashion, Care of Carl has positioned itself as a leading player in the industry, consistently delivering exceptional customer service and high-quality products.
Operating from their headquarters and warehouse just outside Borås, they offer men's fashion to the entire EU through their e-commerce platform, with a presence in local stores in Sweden, Norway, Denmark, Finland, and Germany.
Before implementing Bitlog WMS, Care of Carl relied on traditional pen and paper lists, along with an e-commerce module in their business system. As demand rapidly grew, it became unsustainable to pick orders with printed paper lists, prompting Care of Carl to carefully assess their needs before choosing to implement Bitlog WMS.
Read Magnus' 5 tips for purchasing a WMS >
"I like Bitlog WMS because it is an incredibly user-friendly system."
Magnus Olsson, Head of Logistics, Care of Carl
InstallationLocationBorås, Sweden |
In this videoMagnus Olsson Adam Söderkvist |
Challenges
"Before implementing Bitlog, our picking process was very manual. We relied on pen and paper," shares Magnus Olsson, Head of Logistics at Care of Carl. "We handled all transactions within our ERP-system, which had an e-commerce module, making it incredibly time-consuming."
Magnus describes how the daily operations felt inefficient and challenging to keep track of inventory levels, especially with a steadily increasing demand that quickly became a significant hurdle.
"It was quite chaotic because we had these lists that we picked from," he adds.
Adam Söderkvist, warehouse manager at Care of Carl's Borås warehouse, explains:
"Everything had to be double-checked, we couldn't work based on barcodes like we do today."
With rapid growth and increased demand, managing daily operations became unsustainable for them. Hiring and onboarding new staff proved to be a time-consuming process. They had to pick one order at a time based on paper lists, further delaying the process. It became evident that they needed to implement a WMS - and they ultimately chose Bitlog WMS.
"When we have a lot to do in the warehouse and can't keep up, the office steps in to help with picking, for example. We were limited before when it was manual. Not everyone could handle it. With Bitlog, it's a breeze."
Adam Söderkvist, Warehouse Manager, Care of Carl
The Solution
At Care of Carl, we have successfully integrated Bitlog WMS Advanced together with iPads and handheld scanners to streamline daily operations. This allows for easy and efficient onboarding of new staff who can quickly become self-sufficient. Additionally, the ability to batch pick multiple orders simultaneously enhances the efficiency of the picking process even further.
The implementation of Bitlog WMS at Care of Carl was remarkably swift:
"I think the implementation of Bitlog WMS went incredibly well considering its scale," shared Adam.
Both Adam and Magnus agree that the user-friendly system is easy to get started with, enabling office staff to lend a hand in the warehouse when needed.
"I appreciate Bitlog for its user-friendly interface. It's very straightforward," said Magnus.
Adam added:
"When we have a lot to do in the warehouse and can't keep up, the office steps in to help with picking, for example. We were limited before when it was manual. Not everyone could handle it. With Bitlog, it's a breeze."
Bild: Care of Carl's warehouse in Borås, Sweden.
Results
Compared to the manual processes of the past, Care of Carl has streamlined their operations and increased warehouse efficiency by 40%. The pick and pack stations, in particular, have significantly increased their pace. In addition, they have recorded cost savings of 25% on staffing costs, including salary adjustments over time.
"It's a very positive development," Magnus comments.
The quality of picking has improved substantially with fewer errors and smoother handling of returns. Previously, it was easy to mix up sizes or products, but with Bitlog WMS, the process is now so efficient that such mistakes are nearly non-existent.
"In our return handling, it is crucial to be extremely precise with the sizes received back and sent out [to the warehouse] all the time. Today, with Bitlog, we can simply scan the barcode on the garment," says Adam.
"Today, we can just scan the barcode on the garment, providing us with a highly efficient picking process. There is no need for double-checking, as simply scanning the item will prompt Bitlog to indicate if it's correct or not," adds Magnus and Adam.
Another advantage of Bitlog WMS is access to both real-time data and historical data. Magnus emphasizes that they now have the ability to carry out real-time follow-ups and review past data if they encounter challenges.
"I highly recommend Bitlog for its quick implementation time, ease of understanding for staff, and for businesses like ours with fairly straightforward workflows, it is an extremely beneficial system to implement," concludes Magnus.
You might also like:
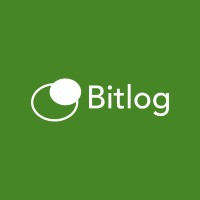
Story by
The Bitlog Team